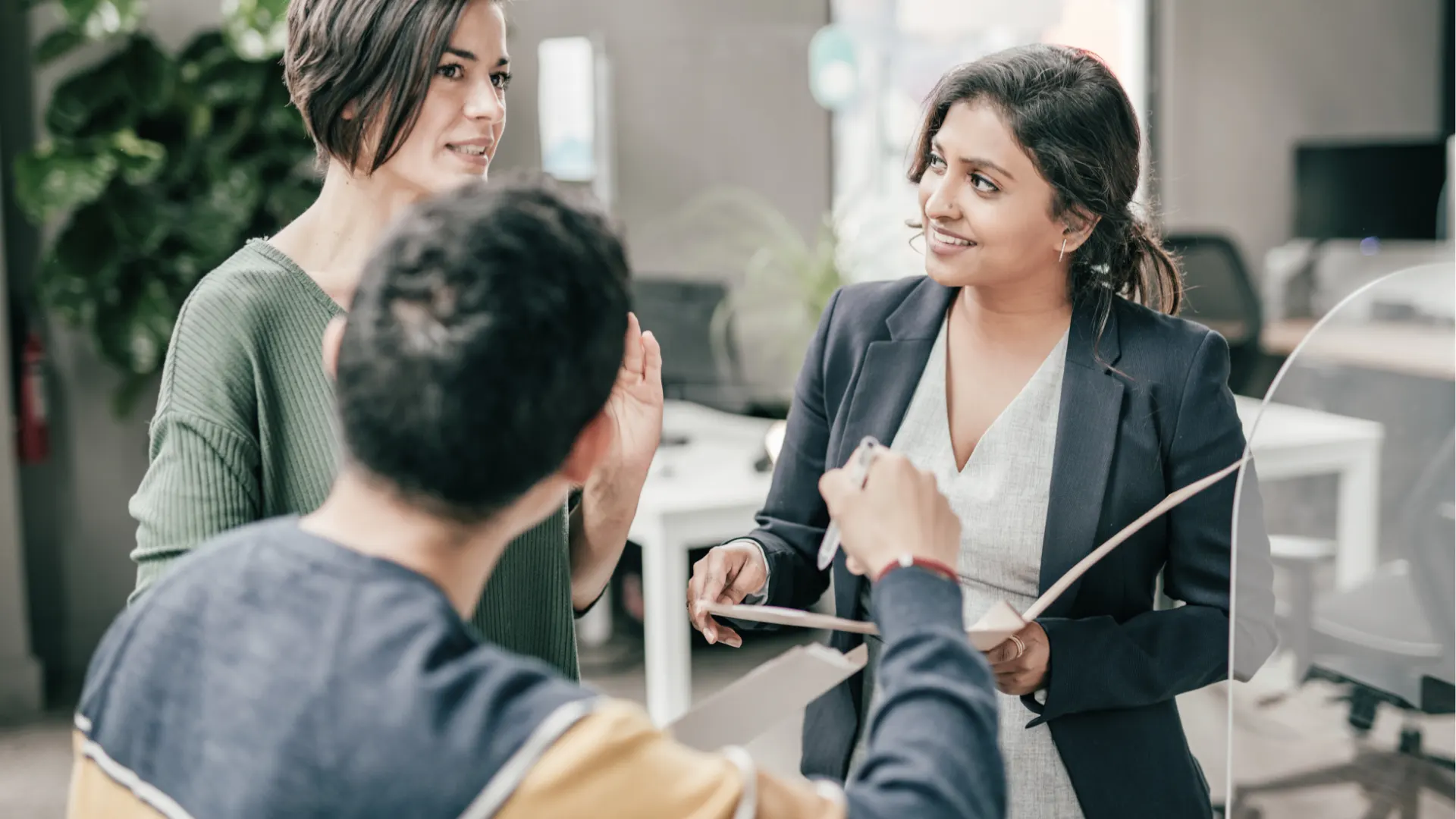
CMMS
Mastering the Art of Asset Management
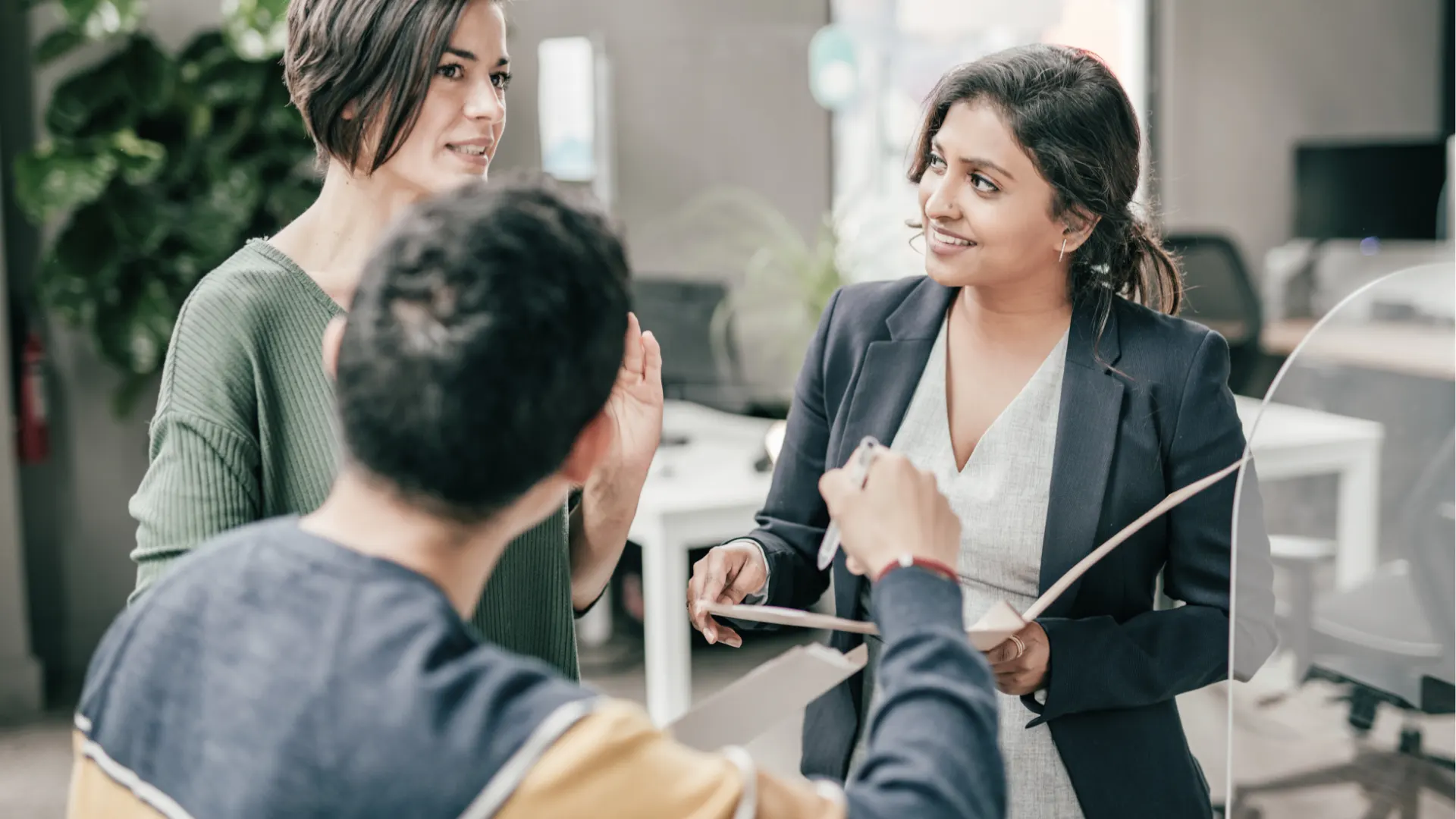
Every day, across all industries, facilities managers are doing the important work of asset management. An asset with a long lifespan is always going to benefit the organization that owns it. Routine maintenance can extend the life of most assets, but there’s always this looming question: Is it time to repair or replace this asset?
Asset depreciation is a real threat to your bottom line, but that doesn’t mean that replacing a system with something new will automatically reduce your expenditures. Facility managers report spending a lot of time weighing the pros and cons of replacing new systems as opposed to keeping older ones alive.
When does it become financially responsible to replace a major asset? At what point is it too costly to perform emergency maintenance on a struggling system?
Today’s retail, warehouse, and restaurant leaders are using state-of-the-art CMMS platforms to improve their asset management practices. Facilities management software, including CMMS, will help you make informed, data-driven decisions about asset replacement vs. repair, instead of having to trust your instincts.
How Do You Determine When to Repair vs. Replace an Asset?
When it’s time to make hard decisions about repairing or replacing any asset, your best option is to go through a careful analysis of multiple factors. The more data you have about the asset’s performance, maintenance history, and associated costs, the more informed your decision can be.
Today’s leading CMMS platforms provide comprehensive data about your assets, including age and performance history, past and ongoing maintenance costs, energy use, and operational impact. The stronger your insights about asset depreciation, the more equipped you will be to make the right choice.
Make sure your CMMS can measure the following in each of those categories:
Asset Age and Performance History
- Current performance against manufacturer specifications
- Maintenance records for patterns of decline
- Whether performance issues are chronic or isolated
Maintenance Costs Over Time
- Repair frequency and associated costs
- Cumulative maintenance expenses
- Replacement cost estimates
Energy Efficiency
- Utility costs associated with the asset
- Efficiency ratings with newer models
- Potential savings from upgraded equipment
Impact on Operations
- Downtime frequency and duration
- Effect on productivity
- Impact on customer experience and satisfaction
This data will help you determine the costs of replacing vs. repairing any asset in one of your facilities.
Signs an asset may need to be replaced include:
- Increasing frequency of repairs
- Rising maintenance costs
- Incompatibility with current or upcoming regulations
- Parts and labor costs keep going up
- Emergency repair needs exceed your planned budget
- Decreased efficiency (higher energy consumption than newer models)
- Difficulty finding replacement parts
- The manufacturer no longer supports this model
Ultimately, the decision to repair or replace is best made with data. A modern CMMS platform can help you track these indicators and make an informed choice, rather than struggling during an emergency to make the right call.
What Are the Cost Considerations in Repair vs. Replacement?
Asset depreciation is costly. Once you have great data, you can calculate the True Cost of Ownership (TCO) of any asset. After all, the cost of installing a new asset is not as simple as the purchase price for the system. You also need to account for:
- Disposal of the current system
- Installation costs
- Operating costs
- Maintenance expenses
- Energy consumption
- End-of-lifespan disposal of the new system
To learn more about TCO, check out our guide to Understanding the True Cost of Facilities Work.
How Can a CMMS Improve Asset Management Decisions?
We’ve already covered the ways in which CMMS can give you better data for informed decision-making. However, a good CMMS can do far more than providing you with good data. At the heart of the issue is that good facilities management software can help you transition from reactive to proactive decision-making.
Let’s take a look at how asset management decisions can be supported by your CMMS in many different ways.
Real-Time Decision Support
Automation escalates emergencies to vendors automatically, which means you don’t have to generate manual service orders. This saves valuable time and minimizes asset downtime. These automated alerts also flag issues before they become critical failures.
You can also use your CMMS’s performance dashboards to enable quick comparisons and data points, even across multiple facilities.
Predictive Maintenance Capabilities
A modern CMMS platform revolutionizes predictive maintenance through sophisticated data analysis and automation. By integrating with IoT (Internet of Things) sensors, you can get real-time performance monitoring of your assets. These sensors feed data directly into your CMMS, which in turn work to identify patterns and potential issues.
If you start getting consistent notifications about potential failures of an asset, you can make those important decisions before things turn disastrous.
A modern CMMS goes beyond simple monitoring, though. The platform can use the data it collects from these sensors to create and maintain automated preventive maintenance schedules. You don’t have to rely strictly on calendar-based maintenance intervals. Instead, these calendars are automatically adjusted based on real usage patterns, performance metrics, and alerts.
Cost Analysis & Budgeting
Your CMMS’s cost analysis tools should allow you to:
- Create detailed tracking of repair costs
- Budget forecasting for replacements
- Conduct ROI analysis for upgrade proposals
- Implement vendor cost comparisons
Learn more about analytics from Fexa!
Workflow Automation
A modern CMMS streamlines operations by automating work order generation, based on the conditions of each asset. This leads to the smart dispatching of appropriate maintenance personnel, whether that’s an internal team member or a contracted skilled tradesperson.
Today’s CMMS platforms are also integrated with procurement systems, which means that parts can be ordered instantly, based on parameters you set within the system.
Additional automated tasks include:
- Tracking warranty information and service contracts
- Monitoring asset depreciation
- Identifying opportunities for bulk replacements
- Supporting capital expenditure planning
The real power of a modern CMMS does not simply lie in data collection, but in the tools’ ability to automate the decision-making process and create asset-supporting workflows. You can eliminate human error and ensure consistent application of maintenance procedures.
What Operational Impacts Should You Consider?
When managing assets, especially when deciding between repairing or replacing them, one of your main goals is to minimize downtime and business disruptions.
Failing assets don’t just cost money through repairs or replacement costs—they also have operational impacts that can cause serious revenue loss. Asset downtime leads to operational downtime, customer frustration, and lost business. If you don’t replace a piece of equipment soon enough, you may end up facing prolonged delays because of issues like supply chain disruptions or installation waiting periods.
Proactive asset management, on the other hand, improves a facility’s efficiency. Here are some of the operational issues to be aware of as you make essential decisions about assets.
Equipment Classification
- Critical vs. non-critical equipment status
- Impact on customer experience
- Role in safety or regulatory compliance
- Interdependencies with other systems
- Backup system availability
Timing
- Seasonal business fluctuations
- Peak vs. off-peak periods
- Weather considerations for installation
- Coordination with other planned maintenance
- Impact on daily operations
- Holiday or special event schedules
Resource Management
- Vendor availability and scheduling
- Internal staff capacity
- Required specialist expertise
- Training requirements for new equipment
- Documentation needs
- Support staff availability
Supply Chain Considerations
- Equipment lead times
- Parts availability
- Shipping and delivery logistics
- Storage requirements
- Installation equipment needs
- Disposal of old equipment
Financial Planning
- Budget cycle alignment
- Cash flow implications
- Fiscal year considerations
- Warranty timing
- Depreciation schedules
- Insurance requirements
Compliance and Documentation
- Permit requirements
- Inspection schedules
- Certification needs
- Documentation updates
- Asset register modifications
- Warranty registration
How to Build a Strategic Asset Management Plan
Unfortunately, some upper-level managers don’t fully appreciate the role of strategic asset management—until bad management brings things screeching to a halt. Creating a strategic asset management plan will prevent that from happening!
Here are 10 pieces of advice for setting up your strategic plan for asset management.
- Invest in facilities management software that supports your organization’s specific and unique needs.
- Plan ahead for repair vs. replace decision-making. By having a framework in place, you can make decisions faster and with more confidence.
- Create a lifecycle management strategy that incorporates preventive maintenance schedules and performance monitoring.
- Establish clear data collection protocols and metrics for asset performance.
- Develop vendor relationships and maintain updated service provider information.
- Implement automated workflows for routine maintenance tasks and inspections.
- Create a comprehensive inventory of all assets with detailed documentation. Your documentation should include equipment specifications, maintenance histories, and warranty information.
- Set up real-time monitoring systems for critical assets. IoT integration can help!
- Establish clear budgeting guidelines for both maintenance and replacement costs. This should include both short-term repair costs and long-term investment planning.
- Develop a training program to ensure all team members understand the asset management system. Regular training updates will help maintain consistency in asset management procedures.
Effective asset management requires data-driven decisions and proactive maintenance. Fexa’s flexible CMMS provides the all the tools you need, from IoT integration and automated workflows to real-time monitoring and vendor management.
Let our purpose-built software help you optimize your assets’ lifecycles and make smarter repair vs. replace decisions. Request a demo today to find out what we can do for your asset management protocols!