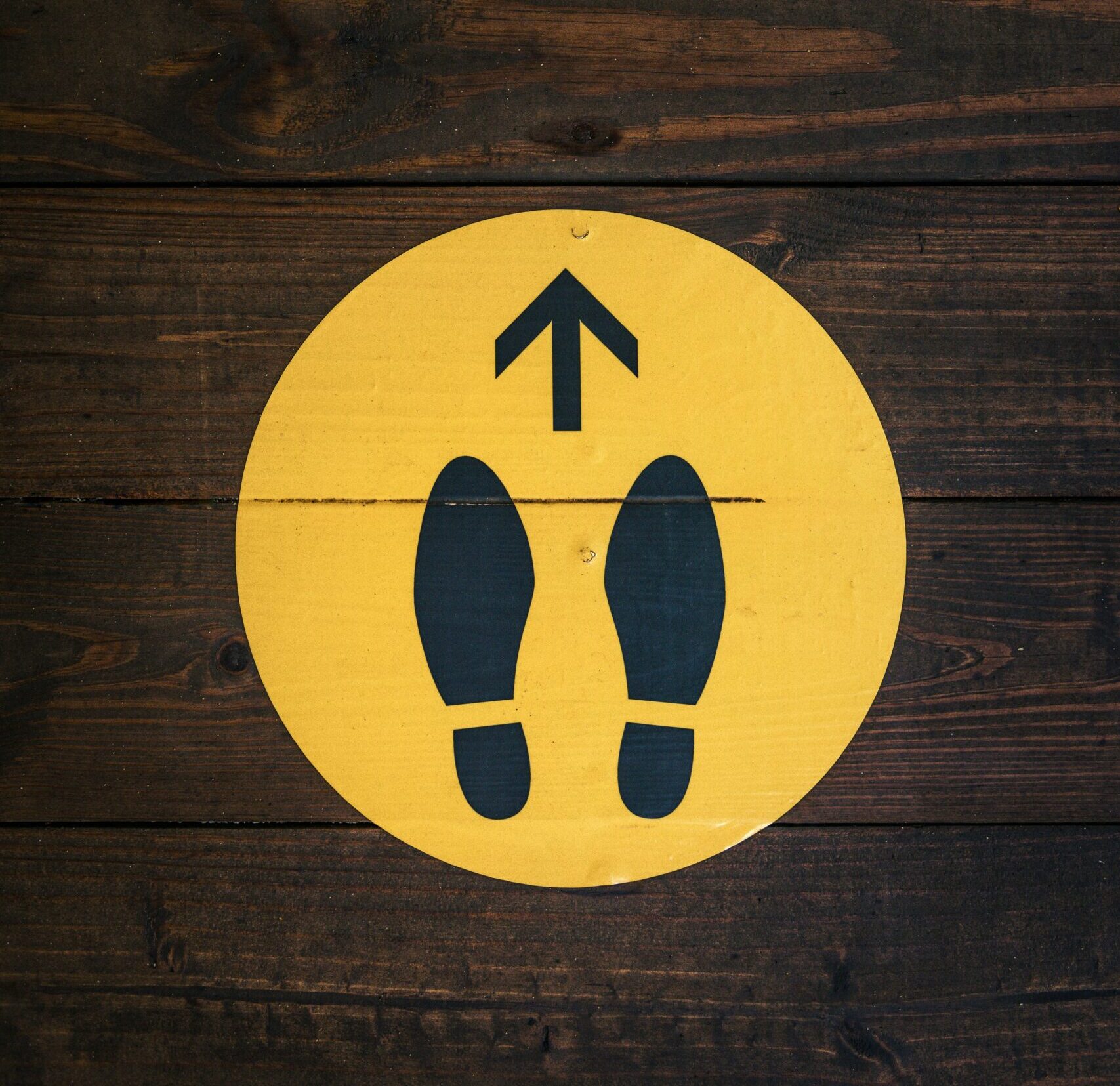
CMMS
Work Order Management: How to Make Work Orders Work For You
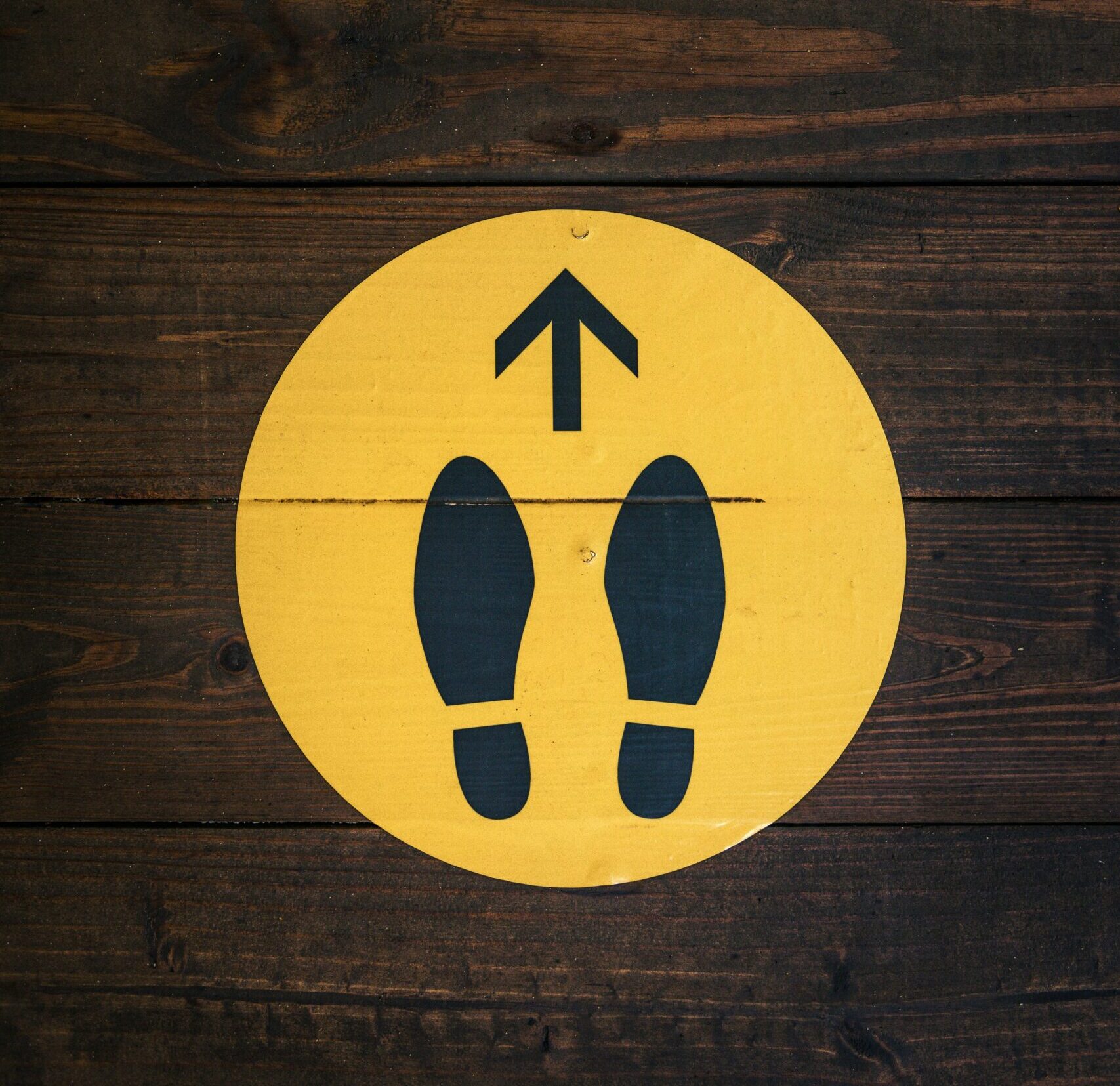
Managing work orders efficiently is a crucial part of facility operations, ensuring that maintenance tasks, repairs, and inspections are performed on time, within budget, and with minimal disruption to business operations. Work order management involves the creation, assignment, tracking, and completion of service requests—whether proactive maintenance or reactive repairs. Let’s explore how effective work order management improves operational efficiency, supports business continuity, and what practices you can put in place to enhance this process.
What is work order management and why is it important?
Work orders represent actionable services within a facility performed by professionals at a specific cost. These can include routine tasks like fire extinguisher inspections or reactive repairs like fixing a broken HVAC unit. Efficient work order management ensures that these services are performed on time and without disruption, protecting the facility’s operations and customer experience.
In facility management, work order management plays a critical role by:
- Improving safety and compliance: Routine inspections, such as fire system checks, help ensure regulatory compliance and maintain safe environments for employees and customers.
- Reducing downtime: Timely repairs and proactive maintenance prevent unexpected equipment failures that could disrupt operations.
- Optimizing resource use: Scheduling tasks during off-peak hours ensures that facilities remain clean, functional, and ready during busy periods. Imagine a restaurant without heating or cooling—it could quickly drive customers away and damage business reputation.
Effective work order management also keeps businesses informed about service providers entering the premises. For example, knowing when a technician will arrive ensures security teams are ready to check them in, avoiding unannounced disruptions.
How to prioritize and automate work orders for maximum efficiency
When managing multiple work orders across various locations, prioritization is key to addressing the most urgent needs first. Emergencies like a non-functioning HVAC system during extreme weather require immediate attention, while routine maintenance can be scheduled in advance during non-peak hours.
Automation plays a significant role in streamlining these processes:
- Predefining vendor relationships ensures the same technicians are assigned to a facility, becoming familiar with its layout and requirements. This reduces onboarding time and enables faster service.
- Automated scheduling and dispatching ensure work orders are assigned to the right technicians based on priority, trade expertise, and availability. This prevents delays and minimizes manual intervention.
- Alert notifications keep all stakeholders updated at every step—from work order creation to technician arrival and completion—ensuring transparency and accountability.
Best practices for assigning and tracking work orders
To manage work orders effectively, follow these best practices:
- Assign vendors based on trade and location: Use primary service providers who are familiar with the facility’s layout and special requirements. This familiarity reduces downtime by enabling quicker diagnosis and repair.
- Track service performance with metrics: Monitor key metrics like turnaround time, first-time fix rate, and completion rates to evaluate vendor performance.
- Implement proactive maintenance plans: Schedule routine maintenance during off-peak times to prevent breakdowns during critical periods.
- Maintain detailed records for tracking warranties and contracts: Ensure repairs are covered under warranties whenever applicable, reducing unnecessary costs.
By following these practices, businesses can enhance operational efficiency and avoid costly disruptions.
The role of CMMS software in work order management
Using a Computerized Maintenance Management System (CMMS) simplifies work order management by consolidating all data and processes into a single platform. CMMS software provides the following advantages:
- Improved Visibility: Centralized dashboards offer a complete view of all active, scheduled, and completed work orders across locations.
- Accurate Reporting: Facility managers can track costs, vendor performance, and repair trends, enabling data-driven decision-making.
- Seamless Vendor Coordination: CMMS tools can automatically dispatch work orders, track service providers, and ensure compliance with special instructions (e.g., insurance requirements or site access protocols).
- Increased Completion Rates: By automating reminders and notifications, CMMS software ensures that tasks are completed on time, reducing the risk of missed deadlines and operational disruptions.
How Fexa can help
Fexa offers a powerful platform designed to streamline work order management and improve facility operations. With Fexa, businesses can:
- Automate vendor assignment and dispatching: Predefine vendors by trade and facility, ensuring the right technicians are assigned quickly and efficiently.
- Customize special instructions for each facility: Include site-specific details, such as parking instructions or roof hatch access, to facilitate smoother service.
- Track every step of the work order process: Receive real-time alerts on technician arrival, service completion, and invoice submission, keeping all stakeholders informed.
- Enhance reporting and analytics: Use Fexa’s dashboards to monitor key metrics like costs, completion rates, and turnaround times, ensuring continuous improvement and better vendor management.
With Fexa’s automation capabilities and easy-to-use platform, businesses can simplify their work order management process, reduce manual effort, and focus on what matters most—keeping their facilities running smoothly and efficiently.
Make work orders work for you with Fexa
Efficient work order management is essential for maintaining safe, functional, and welcoming facilities. By prioritizing and automating tasks, leveraging best practices, and using CMMS solutions like Fexa, businesses can enhance visibility, reduce downtime, and ensure excellent service. With the right strategy in place, work orders don’t just get completed—they work for you.