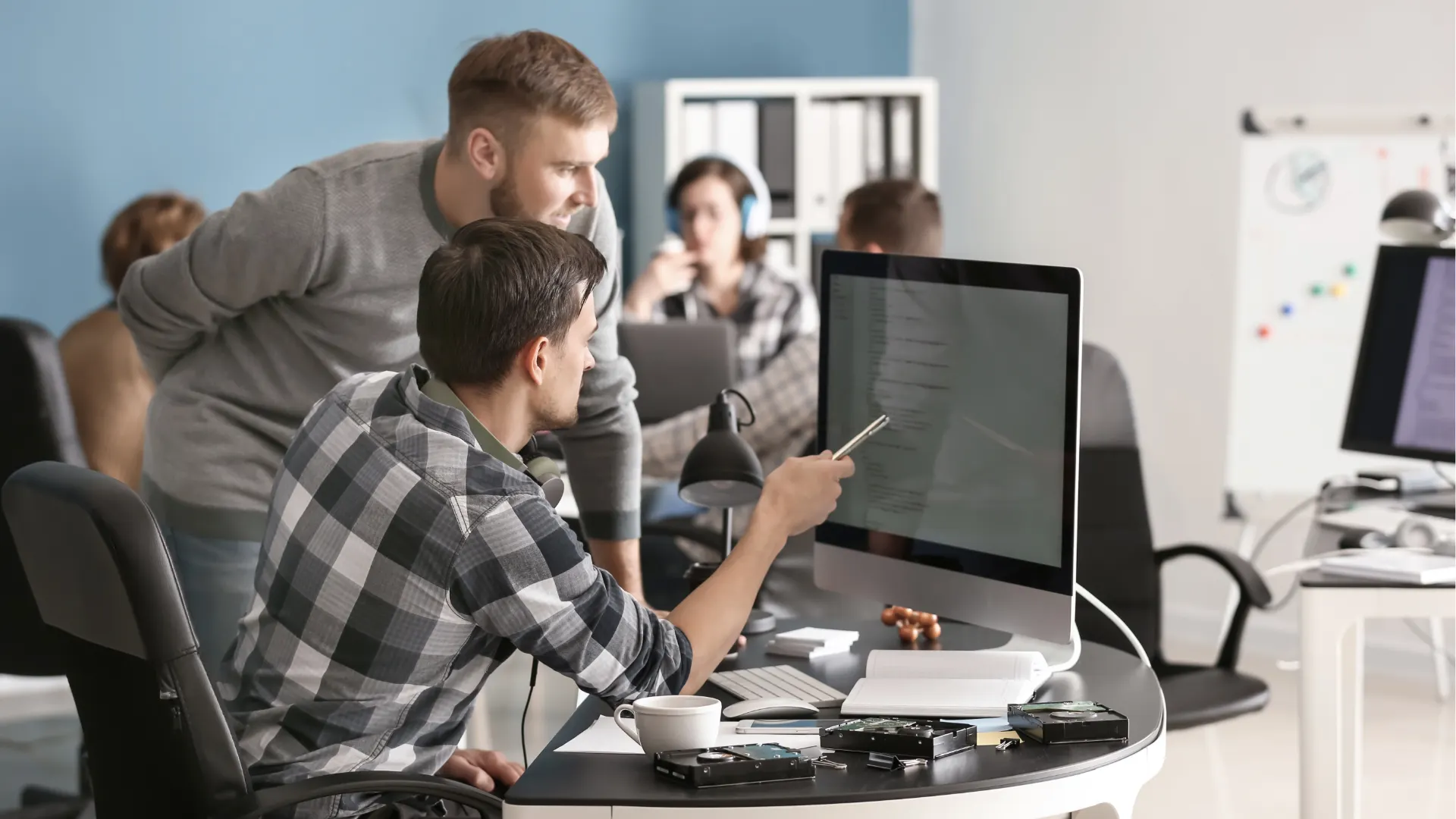
CMMS
How to Build a Preventative Maintenance Plan with CMMS
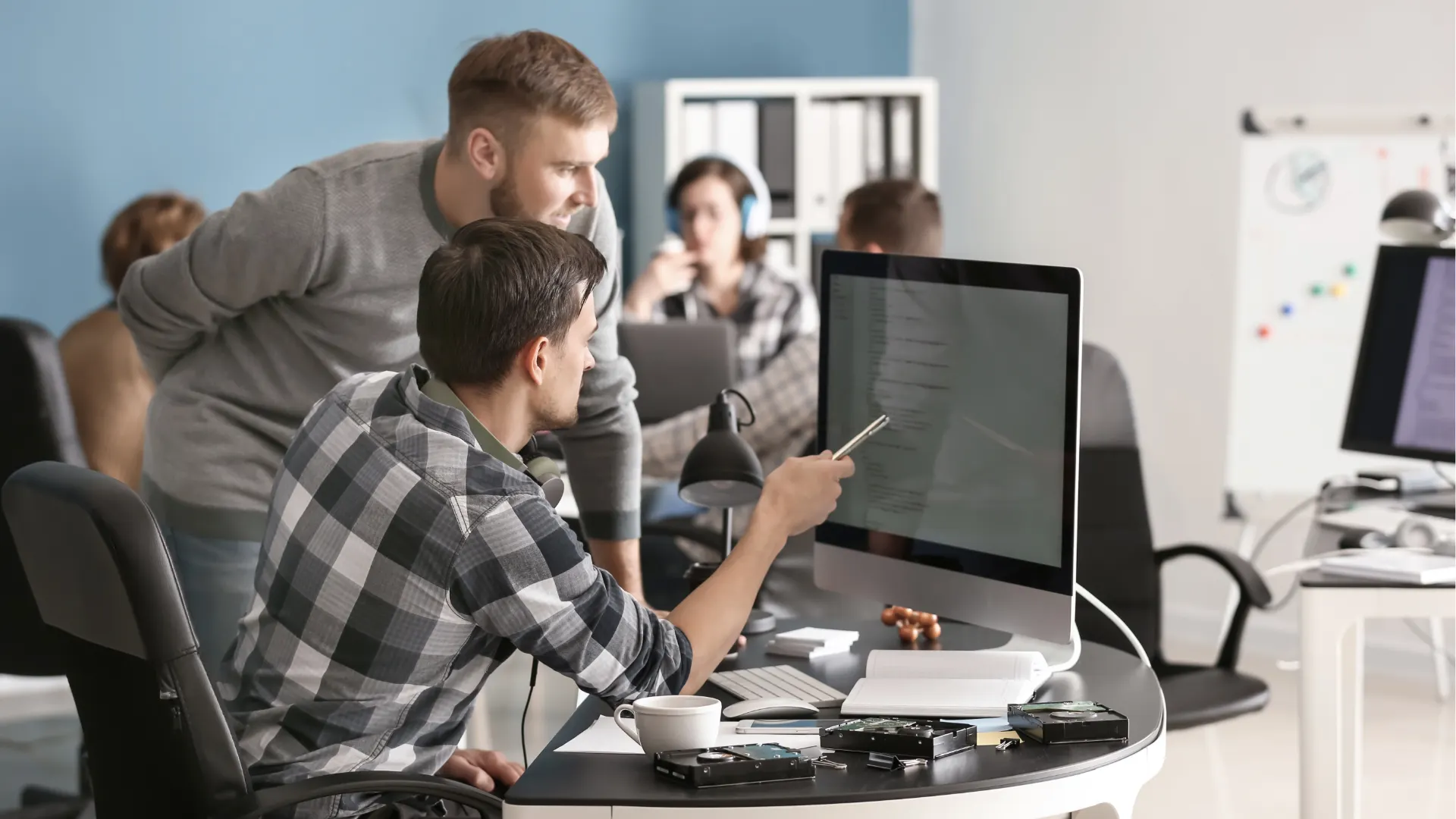
Creating a comprehensive and effective preventative maintenance plan can extend the lifespan of your assets, reduce your total cost of facilities management, and improve your bottom line. The challenge is this: How do you design and implement a preventive maintenance plan that works?
The answer is to use a flexible CMMS that is configured to meet your exact and unique needs. Using the power of automation, strategic asset management, and data-driven decision-making, your CMMS can turn a haphazard approach to predictive maintenance into a well-oiled machine.
Let Fexa guide you through the process of creating a CMMS-driven preventative maintenance plan that you can start implementing right away.
Understanding Preventive Maintenance
Before you can build a solid preventive maintenance plan, it is important to understand why it’s so important to have one.
Preventive maintenance (PM) is a proactive approach to facility management that focuses on preventing equipment failures before they have a chance to occur. This is in contrast to reactive maintenance, which occurs when you have to respond to unplanned breakdowns.
A highly functioning PM strategy has been shown to extend the life of your assets, reduce total operational costs, and improve facility reliability. Equipment downtime can wreck your revenue, especially if it causes closures or delays that affect customers.
Making a PM plan, then, allows you to systemize your approach to predictive maintenance. Instead of responding to one crisis after another, your PM plan can keep your systems operational for longer. Facilities management software like CMMS can support your approach to PM.
Cost benefits of preventative maintenance
Organizations that implement robust preventive maintenance programs typically see:
- Reduced emergency repair costs
- Extended equipment lifecycles
- Lower total cost of ownership
- Improved energy efficiency
What assets should be included in a preventive maintenance plan?
Let’s look more closely at what assets should be included in your PM plan. This is not a comprehensive list—but it’s close! We’ve categorized these assets into groups based on function.
HVAC/R Systems
- Commercial air conditioning units
- Industrial refrigeration systems
- Heating systems
- Ventilation equipment
- Cooling towers
- Chillers
Safety and Compliance Equipment
- Fire suppression systems
- Emergency lighting
- Fire extinguishers
- Alarm systems
- Backflow systems
- Safety sensors and monitors
Building Infrastructure
- Electrical systems
- Plumbing systems
- Building envelope components
- Structural elements
- Elevators and escalators
- Generators
Assets in Retail Environments
- Point of sale systems
- Security systems
- Lighting systems
- Display cases
- Shopping carts
- Loading dock equipment
Food Service Operations Assets
- Commercial kitchen equipment
- Walk-in coolers and freezers
- Food preparation surfaces
- Ventilation hoods
- Dishwashing systems
- Food storage equipment
Building Automation
- Smart building controls
- Energy management systems
- Access control systems
- Security cameras
- Automated lighting
- Climate control systems
IT Infrastructure
- Server rooms
- Network equipment
- Data centers
- UPS systems
- Communication systems
- Emergency backup systems (“The Essential Guide to Facilities Technology”)
Determining which assets should be prioritized
Every facility manager would be thrilled if they could start fresh, with every task completed at once. Unfortunately, that’s not the reality of the job. When you’re using your CMMS to develop a PM plan, you have to prioritize which assets need attention now vs. which ones can wait a little longer.
That’s why you must conduct a critical asset assessment. This is your opportunity to identify the highest-priority concerns in your operations.
Consider these factors:
- What is the asset’s impact on your operations? Consider the effect on your core business functions if this asset goes down. The cost of downtime should also include the impact on customer experience. If you inconvenience a customer, you could lose them forever, which means that the loss extends far beyond the initial downtime. Preventative maintenance protects you from those losses.
- What are the safety and compliance risks of waiting to address the issue? This includes considering the regulatory requirements and safety implications of ongoing problems. Some assets have a larger environmental impact than others, whereas others present liability exposure.
- What is the asset’s value? This includes:
- Replacement cost
- Remaining useful life
- Depreciation schedule
- Maintenance vs. replacement cost ratio
- What are the current operating costs of the asset? This includes:
- Energy consumption
- Maintenance expenses
- Labor requirements
- Parts and supplies costs
Use your CMMS to drill down on data points that give you insights into every asset and the costs associated with keeping it operational.
The practical application of this information is to divide your assets into three priority groups.
High-priority assets meet the following criteria:
- Critical to core operations
- High replacement cost
- Safety-related equipment
- Regulatory compliance requirements
- Revenue-generating equipment
Medium-priority assets include assets that:
- Support core operations
- Have moderate replacement costs
- Affect customer experience
- Impact employee productivity
Lower-priority assets are generally going to:
- Have minimal operational impact
- Are easily replaceable
- Have low maintenance costs
- Provide auxiliary functions that are important but not necessarily essential
Determining the Right Maintenance Intervals
Once you know which assets need to be prioritized for preventative maintenance, you can use data from your CMMS to determine the right maintenance intervals for each one.
These are the three key data sources that you will pull from your CMMS to choose intervals:
- Historic performance data (failure history, maintenance records, repair costs)
- Manufacturer guidelines and recommendations
- Real-time monitoring and IoT sensor data
Historic performance data
Facilities data from your CMMS is your best friend in this process.
This important data provides insights into how your equipment has actually performed in your specific environment. This includes not just failure history, but also the effectiveness of past maintenance efforts and their associated costs.
Manufacturer guidelines
Manufacturer guidelines serve as an important baseline, though they should be viewed as a starting point rather than an absolute rule. These recommendations typically err on the conservative side and may need adjustment based on your specific operating conditions.
Real-time monitoring and IoT sensor data
IoT sensors provide real-time data about the performance of each piece of equipment in your catalog. This includes metrics like temperature, vibration, energy consumption, refrigerant levels, operating conditions, and more. By providing you with a continuous stream of data, these sensors allow you to spot potential issues before they become failures.
Setting up a calendar for regular maintenance intervals is important, but IoT sensors allow you to quickly respond to conditions that could lead to equipment failure.
Other factors affecting maintenance intervals
Other factors that may affect how often you should perform routine maintenance include:
- Asset criticality and its impact on operations
- Direct maintenance costs (labor, parts, materials)
- Indirect costs (downtime, lost revenue, customer impact)
- Environmental conditions and usage patterns
- Regulatory requirements and compliance needs
The right balance depends heavily on understanding your asset’s criticality. High-priority assets that directly impact safety, regulatory compliance, or core business operations may warrant more frequent maintenance despite higher costs.
The Role of CMMS in Preventive Maintenance
As the leading provider of flexible CMMS solutions here at Fexa, we are excited to share just how much a great CMMS platform can support your preventative maintenance goals! We couldn’t possibly go over all of the key features of a fully customized CMMS in a single blog post, but we’ll cover some of the most exciting ones.
Core Automation Functions of a CMMS
First, let’s talk about automation.
A modern CMMS transforms preventive maintenance from a manual, time-consuming process into a streamlined, automated system. By leveraging smart automation, facilities teams can eliminate repetitive tasks and focus on strategic decision-making.
Key automation capabilities include:
- Automatic work order generation based on preset triggers
- Smart dispatch routing to appropriate technicians
- Real-time status updates and notifications
- Automated compliance checks and documentation
- Warranty validation and tracking
Data-Driven Decision Making
Decisions are better when they are built on solid, actionable data. Your CMMS is the tool that can give you that data.
Think of your CMMS platform as a centralized data hub that captures and analyzes maintenance information across every single facility in your organization. This comprehensive data collection enables facilities managers to make more informed decisions about maintenance timing and resource allocation.
You can collect data on metrics like these:
- Mean time between failures
- Cost per maintenance hour
- Asset performance trends
- Resource utilization rates
- Compliance status
Workflow Management
Next, CMMS platforms optimize maintenance workflows by creating standardized processes while maintaining flexibility for unique business needs. The system can automatically adjust asset management workflows based on various factors like asset type, location, or urgency level.
Critical workflow features include:
- Custom field creation for specific tracking needs
- Automated approval routing
- Priority-based task assignment
- Resource allocation optimization
- Multi-site coordination
Additional Data Sources from Your CMMS
Some of the additional data points that you can get from your CMMS include:
- Technician performance metrics
- Time and labor tracking for job completion
- Accurate records of exact tasks performed during each maintenance encounter
- Thorough asset history tracking
- Parts usage and costs
- Asset performance metrics
- Compliance requirements
- Regulatory reporting obligations
- Budget tracking
- ROI calculation
Fexa is the Optimal Solution for Preventive Maintenance
Fexa stands out from other CMMS providers, including legacy companies, by offering the most configurable platform on the market.
The Fexa software solution adapts to your specific operational needs. Rather than forcing your business to conform to rigid solutions that are based on some other organization’s needs, Fexa is tailor-made to your operations. We are proud to offer fast response times and unmatched flexibility in responding to your needs.
Fexa’s CMMS provides you with the data you need to develop a highly functional predictive maintenance plan. Our platform goes beyond simple facility management software solutions to give you:
- Smart project management for complex, multi-trade projects
- Vendor management without hidden fees or forced provider networks
- Automated compliance tracking, including specialized tools like Trakref for refrigerant management
- Custom fields and workflow automation to match your specific processes
Check out more information about the financial and operational benefits of switching to Fexa’s CMMS. Fexa’s forward-thinking approach ensures that your preventive maintenance program can help you thrive in the present and respond nimbly to challenges that arise in the future. Contact Fexa for a free demonstration today—Let us show you what we can do!