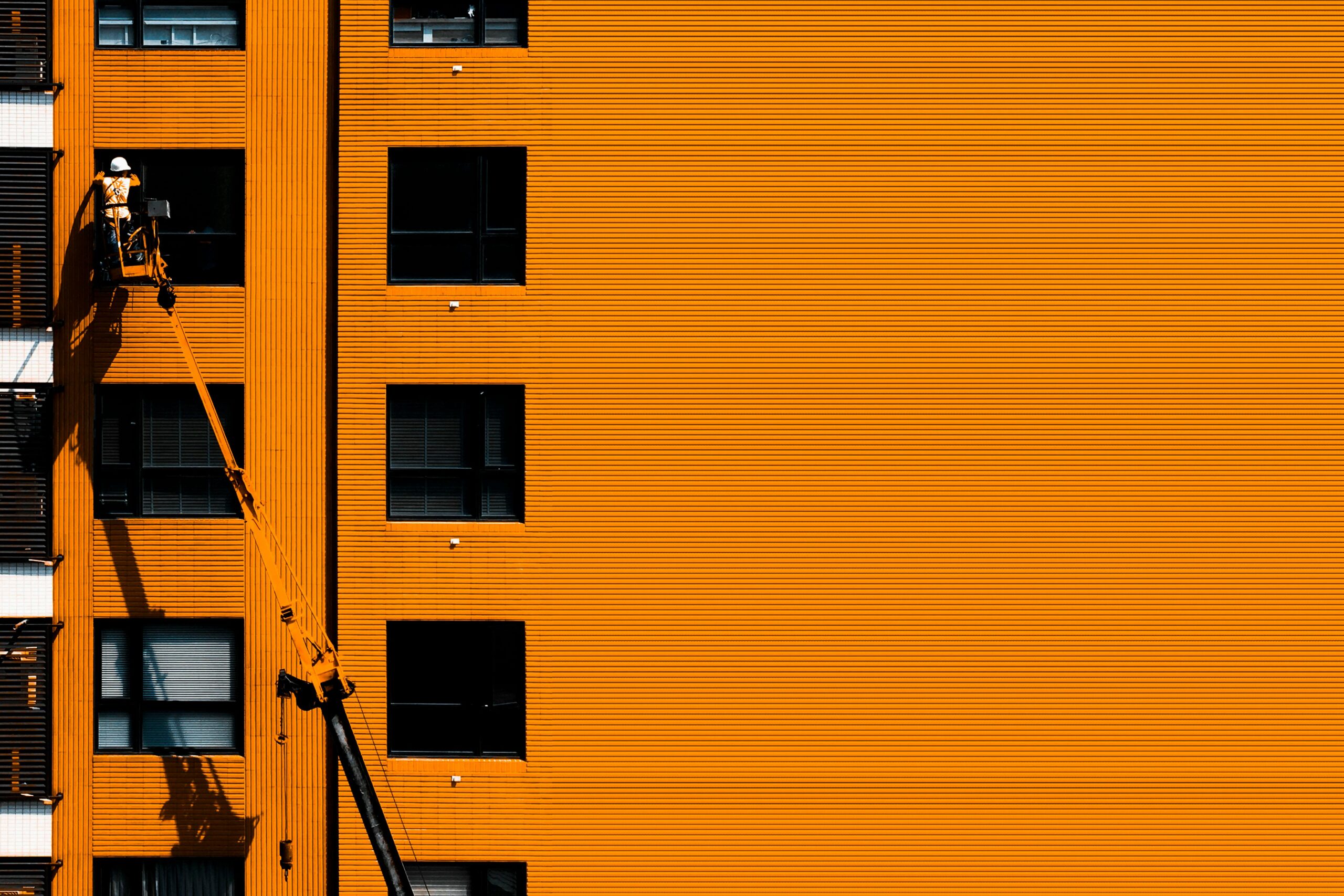
CMMS
Power of Prevention: How Preventative Maintenance and Asset Tracking Saves Time and Money
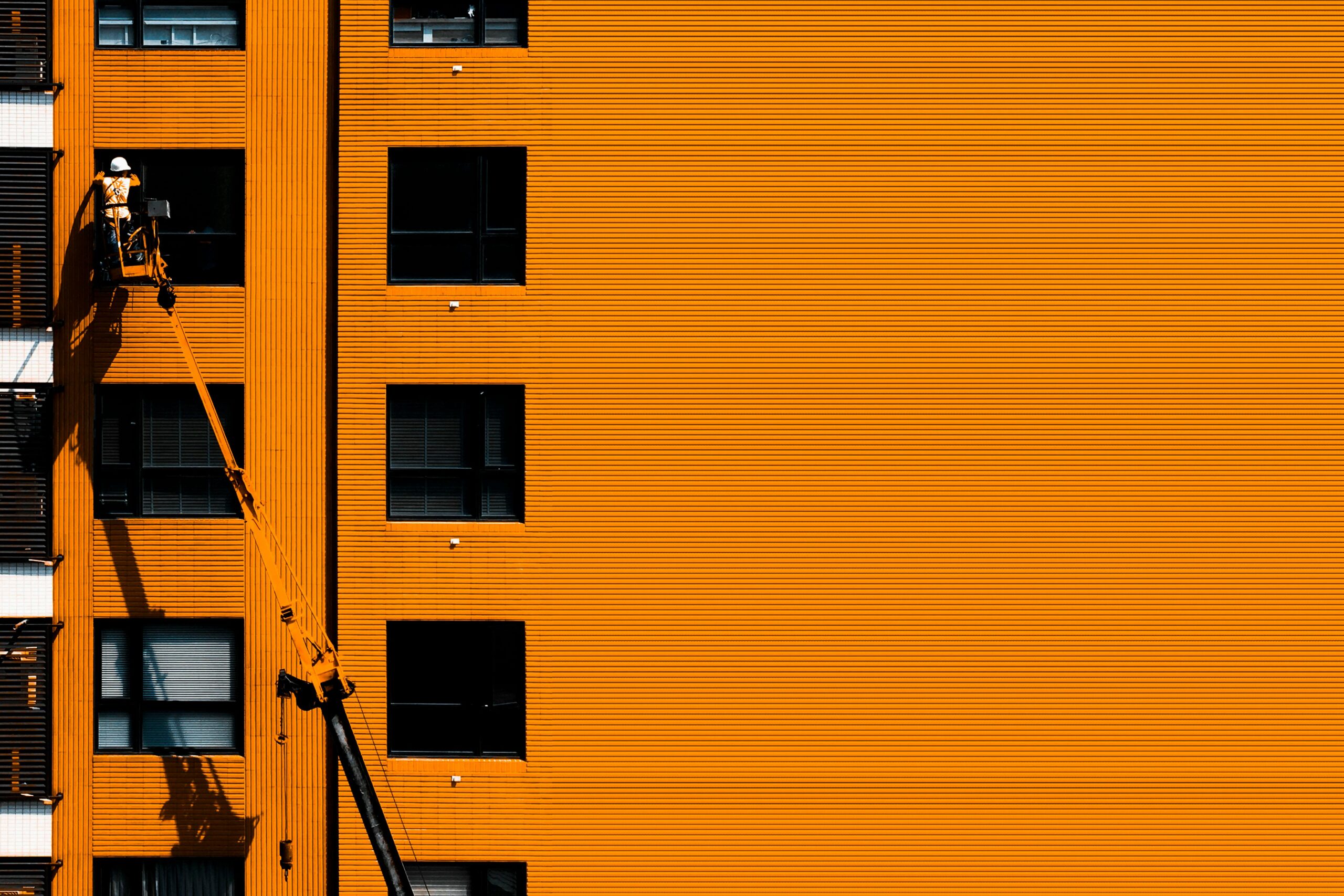
Facility management is a complex operation that requires a balance between keeping everything running smoothly and controlling costs. One of the most helpful ways to achieve this balance is through preventative maintenance (PM) combined with robust asset tracking.
This approach extends the life of your equipment, saves time and money by avoiding expensive repairs, and makes decision-making easier. Let’s take a closer look at how preventative maintenance and asset tracking can level up your facility management operations.
The Role of Preventative Maintenance in Facility Management
Preventative maintenance plays a critical role in keeping facilities and equipment operating efficiently. Unlike reactive maintenance, which involves responding to equipment failures as they occur, preventative maintenance is all about anticipation and preparation. By scheduling routine servicing and inspections, facility managers can catch potential issues before they escalate into costly problems.
For example, scheduled inspections—such as checking fire extinguishers, alarms, and backflow systems—ensure critical safety systems are always functional. Similarly, routine maintenance on equipment like HVAC systems, including seasonal services like filter changes and system checks, ensures optimal performance, especially during high-demand seasons. Services like winterization and de-winterization of external water sources are essential to prevent freezing or damage during colder months.
Regular recurring services, such as janitorial cleaning, pest control, and power washing, also fall under preventative maintenance. These services help to maintain not just the cleanliness of the facility but also the health and safety of all occupants. By implementing these practices, facilities can avoid unplanned breakdowns, extend equipment life, and reduce emergency repair costs.
The Benefits of Asset Tracking
Asset tracking goes hand-in-hand with preventative maintenance. Knowing where your assets are, what condition they’re in, and how much they cost to maintain gives facility managers unprecedented control and visibility.
With formal documentation of each asset and equipment, facility managers can reliably store detailed information, such as model numbers, purchase dates, and even warranties. Tracking real-time data allows managers to identify which assets are nearing the end of their lifecycle, thus enabling more strategic decisions on repair versus replacement.
Reportable service history is another powerful advantage. The ability to look at the complete maintenance history of an asset—along with associated costs—provides insights into recurring issues, helping to pinpoint equipment that is underperforming or frequently breaking down. This data allows for better budgeting and resource allocation, especially when you can track the depreciation of an asset over time, and analyze when it becomes more cost-effective to replace it rather than continue repairs.
The ever-changing regulatory landscape will also require record tracking in the event of an incident, making it crucial to prepare your asset data in a way that allows you to track specific data points. This proactive approach not only ensures compliance but also sets you up for future success when regulations evolve.
Asset tracking also significantly improves accountability. Knowing exactly where your assets are located and which ones are due for maintenance or replacement reduces the likelihood of overlooked inspections or delayed repairs. With all identifying information and maintenance history at hand, facility managers can ensure that maintenance teams are equipped to handle repairs efficiently and accurately.
The Benefits of Combining Preventative Maintenance & Asset Tracking
When preventative maintenance is combined with asset tracking, the advantages become even more pronounced. For instance, maintenance service history can be applied directly to an asset, allowing facility managers to track the costs of all preventative maintenance tasks against the asset itself. This integration enables a complete view of how much has been spent on an asset and how it has performed over time, providing critical insights into its cost-effectiveness.
Combining the two also offers proof of service history, which is crucial for compliance with warranty requirements. Many warranties require evidence that regular maintenance has been performed to remain valid. With integrated asset tracking and preventative maintenance, this documentation is readily available.
In addition, this approach is essential for ensuring compliance with HVAC/R regulations that mandate a history of preventative leak inspection services tied to the associated assets. By prepping this data now, companies can streamline compliance and set themselves up for success in the long term, especially as regulations evolve.
Success Story: Solidcore’s Efficient Asset Management
A prime example of the power of preventative maintenance and asset tracking comes from Fexa’s customer, Solidcore. By using Fexa’s asset tagging feature, Solidcore was able to streamline the way they manage their assets. For instance, a facility manager can scan an asset’s QR code using a mobile device, which pulls up detailed information about that asset. From there, they can quickly create a work order specifically tied to that asset.
This process ensures that the asset’s service history is updated in real time, and the system will even notify the user if the asset is still under warranty. This level of automation eliminates the need for manual tracking and ensures that work orders are always accurately associated with the right equipment. Solidcore has also applied this asset management system to their HVAC maintenance program, ensuring that their HVAC units are maintained regularly without needing to rely on cumbersome spreadsheets.
“We use Fexa for all of our work order maintenance, and we love it. All of our studio managers use it, and so we have all of our vendor partners use it as well. We refuse to work with anybody who doesn’t use it. It’s really helpful for us to have a platform that has everything. The notes sections are great with communicating, having the proposals and invoices all in one platform is really helpful. It’s been really convenient to use. What we like most about Fexa is really just how user-friendly it is. The fact that anybody can use it, it’s really intuitive.”
— Jaclyn Gould, Senior Manager of Facilities & Equipment, [solidcore]
How Fexa Can Help
Fexa offers a comprehensive suite of tools that integrates preventative maintenance with advanced asset tracking, helping organizations manage their facilities more effectively. And when combined with Trakref for refrigerant management, you get an even more powerful system to ensure compliance and sustainability in HVAC operations.
Assets & Asset Tagging
With Fexa, you can tag assets with QR codes for easy access to information and service history. This ensures that work orders and maintenance tasks are always linked to the right equipment.
Asset Warranty Tracking
Fexa allows you to track warranties, ensuring that any repairs or replacements are covered if applicable.
PM Programs
Fexa’s PM programs operate on a “set it and forget it” principle, automating recurring maintenance tasks based on a pre-determined schedule. This reduces manual intervention and guarantees consistency in preventative maintenance tasks.
Cost Allocation & Depreciation Views
Track the costs associated with each asset and view depreciation trends, which helps you make informed decisions about when it’s time to replace aging equipment.
Advanced Analytics Reporting
Fexa’s reporting tools provide valuable insights into the performance of your preventative maintenance (PM) programs and assets. Through these advanced analytics, facility managers can track services completed vs. open work orders, identify assets with recurring issues, and analyze how the PM program is affecting overall operational efficiency. This data-driven approach, combined with Trakref’s refrigerant tracking and compliance features, helps organizations spot inefficiencies, stay compliant, and improve their processes.
A Unified Approach to Facility Management
Combining preventative maintenance with asset tracking in a unified system like Fexa is the key to optimizing facility management. It ensures that assets are maintained proactively, reducing the likelihood of costly breakdowns and improving the longevity of equipment. Asset tracking also provides essential real-time insights into the condition and history of equipment, allowing for more strategic decision-making, including when to repair or replace assets.
With automated PM programs and detailed asset tracking features, Fexa empowers facility managers to save time, reduce costs, and enhance productivity. Instead of dealing with manual processes, outdated spreadsheets, and unreliable records, Fexa offers a comprehensive, user-friendly solution to manage maintenance and assets seamlessly.