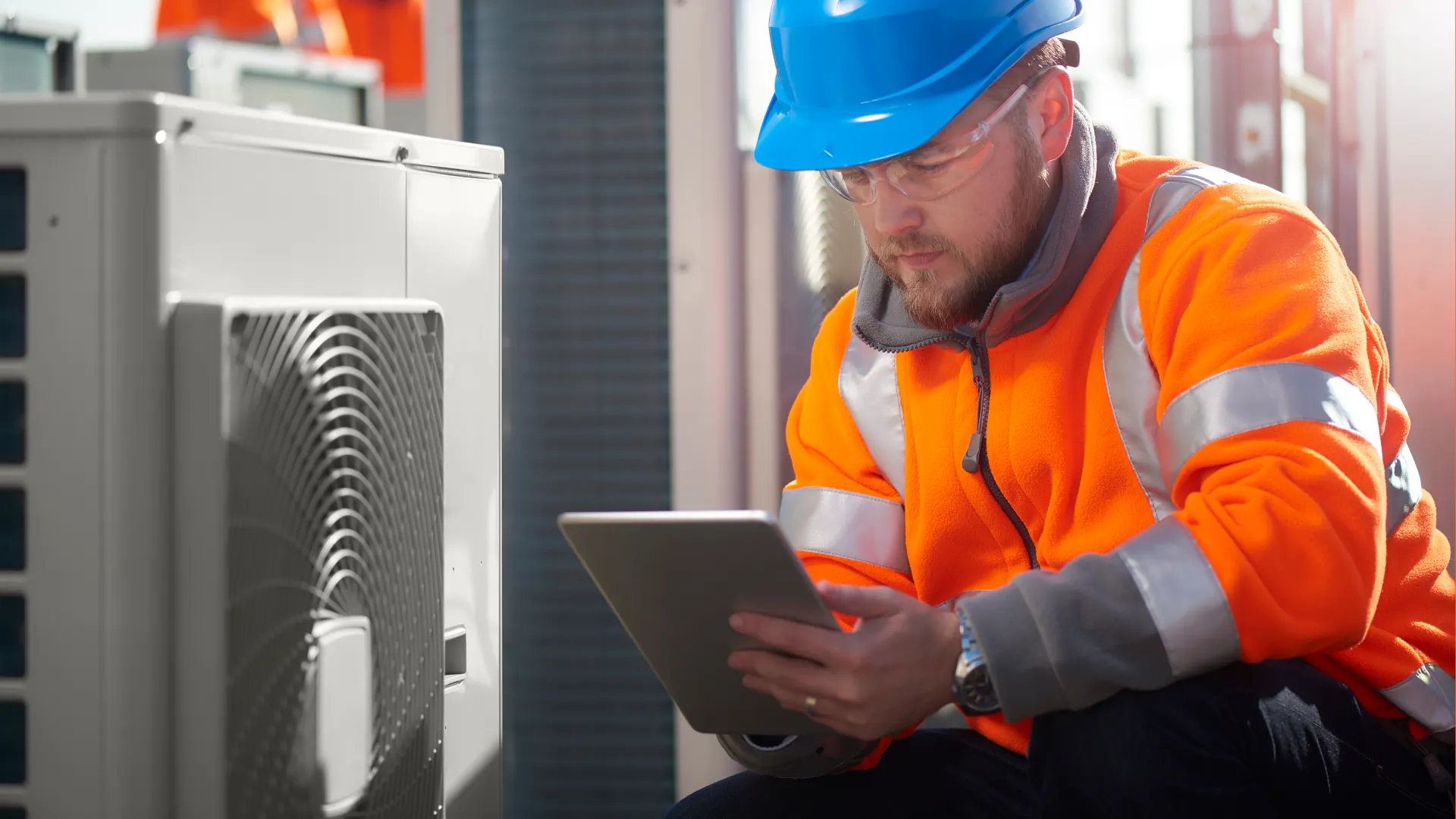
CMMS,
What Is Preventive Maintenance? (Definition, Benefits, and How It Works)
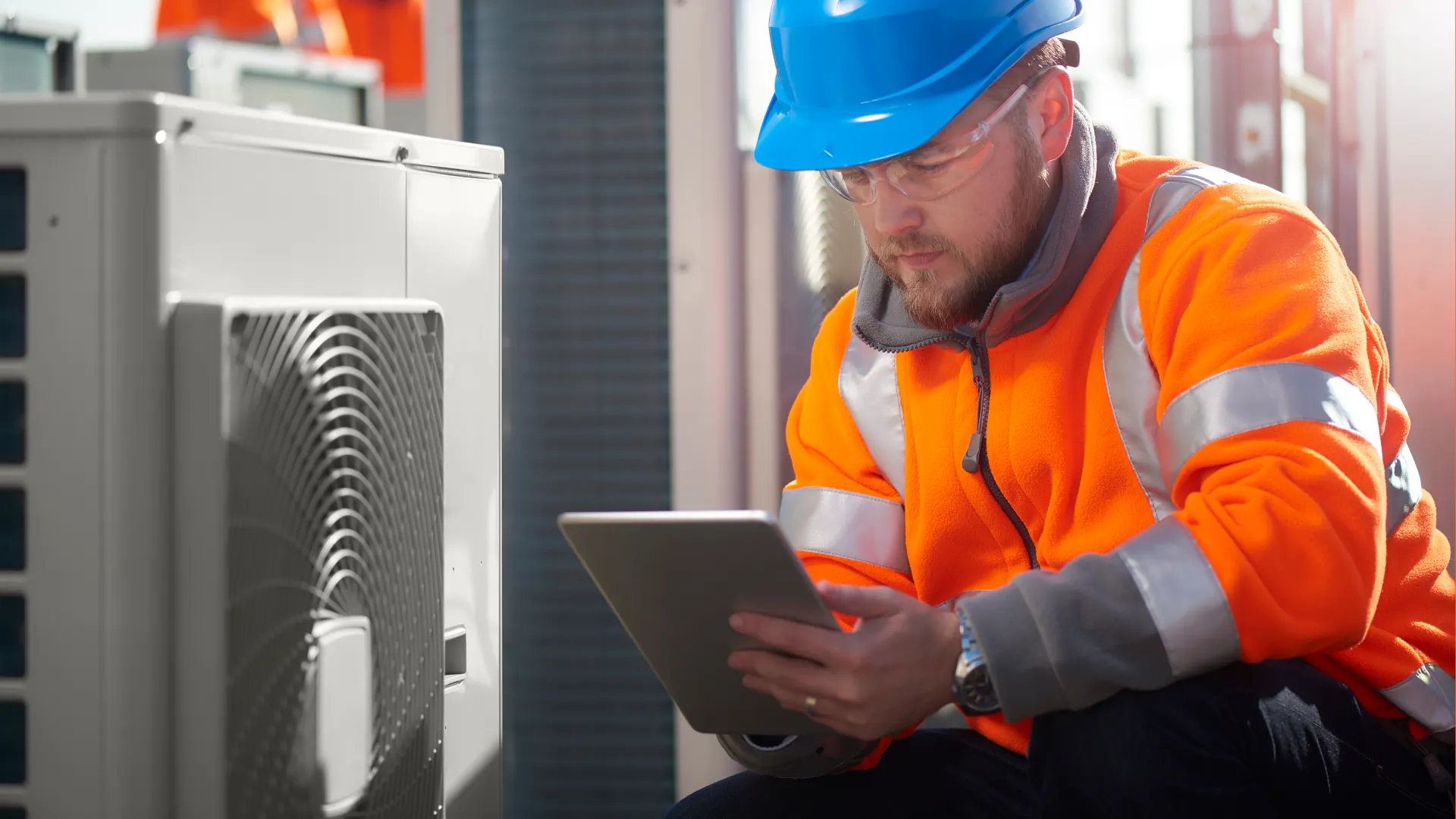
Preventive maintenance is a cornerstone of modern facilities management—and for good reason. Rather than waiting for things to break, this strategy is all about keeping assets running smoothly through routine care. It’s proactive, structured, and it saves money, time, and stress in the long run. If you’re looking to improve reliability and reduce downtime, this Preventative Maintenance Guide is a great place to start. And if you’re ready to take action, Fexa’s Preventive Maintenance Solution can help you implement best practices at scale.
Routine maintenance also supports data-driven improvements. Learn how preventive maintenance and asset tracking save time and money across industries by reducing surprise failures and maximizing ROI.
In this blog, we examine what preventive maintenance entails, and how it compares to other maintenance approaches.
What is preventive maintenance and how does it work?
Preventive maintenance (often shortened to PM) is the practice of performing regular, scheduled upkeep on equipment and systems to prevent unexpected breakdowns. Think of it as a routine check-up for your building’s most critical assets: HVAC systems, plumbing, electrical infrastructure, fire suppression systems, and more.
This approach involves tasks like inspections, cleaning, lubrication, and minor repairs—all done on a set schedule, whether that’s weekly, monthly, or quarterly. By addressing issues early, PM keeps small problems from snowballing into major failures that disrupt operations and require costly emergency fixes.
How is preventive maintenance different from predictive and reactive strategies?
Preventive maintenance is often confused with predictive maintenance, but the two are distinct. Predictive maintenance relies on data from IoT sensors and analytics tools to determine when service is needed based on equipment performance trends. It’s more dynamic and tech-intensive but ideal for critical assets that require continuous uptime.
Reactive maintenance, on the other hand, is what happens when something breaks—and then gets fixed. It’s the most expensive and disruptive option because failures are unexpected and often urgent.
The best strategy typically blends preventive and predictive approaches, reserving reactive responses for true emergencies.
What types of assets benefit most from a preventive maintenance approach?
While predictive maintenance is a smart choice for high-value or mission-critical equipment, preventive maintenance is ideal for a wide range of facility assets—especially those with predictable wear patterns. These include:
- HVAC and refrigeration units
- Electrical panels and lighting systems
- Plumbing and piping infrastructure
- Fire and safety systems
- Doors, elevators, and mechanical equipment
Regular servicing of these assets helps ensure operational continuity, energy efficiency, and compliance with safety standards.
What are the most common examples of preventive maintenance tasks in facilities?
The exact tasks vary depending on the asset, but most preventive maintenance programs include:
- Lubrication of moving parts
- Air filter replacements
- Equipment calibration
- Leak detection and repair
- Battery testing and replacements
- Inspection of belts, bearings, and electrical connections
- Cleaning and sanitation of HVAC coils or ducts
These activities, while relatively minor on their own, add up to significant savings and reliability over time.
How can CMMS platforms support a successful preventive maintenance program?
A modern Computerized Maintenance Management System (CMMS) like Fexa transforms preventive maintenance from a paper-based chore into a streamlined, data-driven strategy. Key benefits include:
- Automated work order generation
- Centralized tracking of asset history and warranties
- Inventory and parts management
- Mobile access for field technicians
- Real-time dashboards and reporting
CMMS platforms also help enforce compliance, track technician performance, and optimize scheduling, ensuring that maintenance tasks are done on time and with minimal disruption.
Wondering which data points to track? Here’s a guide on what metrics your CMMS should be tracking. These insights can help shape your strategy and ensure accountability.
Build a smarter maintenance program with Fexa
Preventive maintenance is more than a checklist—it’s a strategic investment in the long-term health and efficiency of your facility. With the right tools and schedule in place, you can cut costs, reduce downtime, and extend the life of your assets.
Learn more about Fexa’s Preventive Maintenance Solution: https://fexa.io/preventative-maintenance