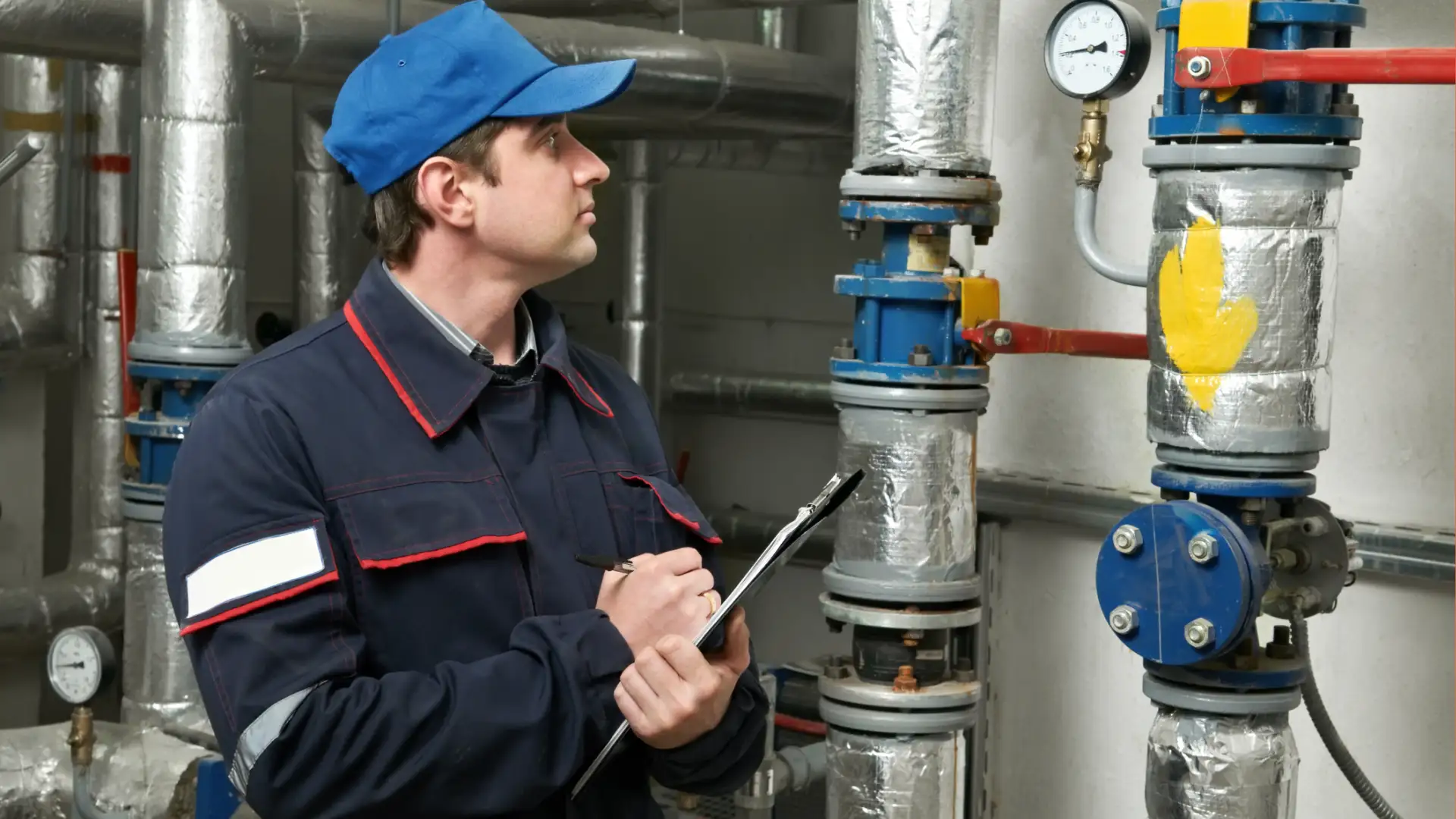
CMMS
Why Preventive Maintenance Matters in Facilities Management
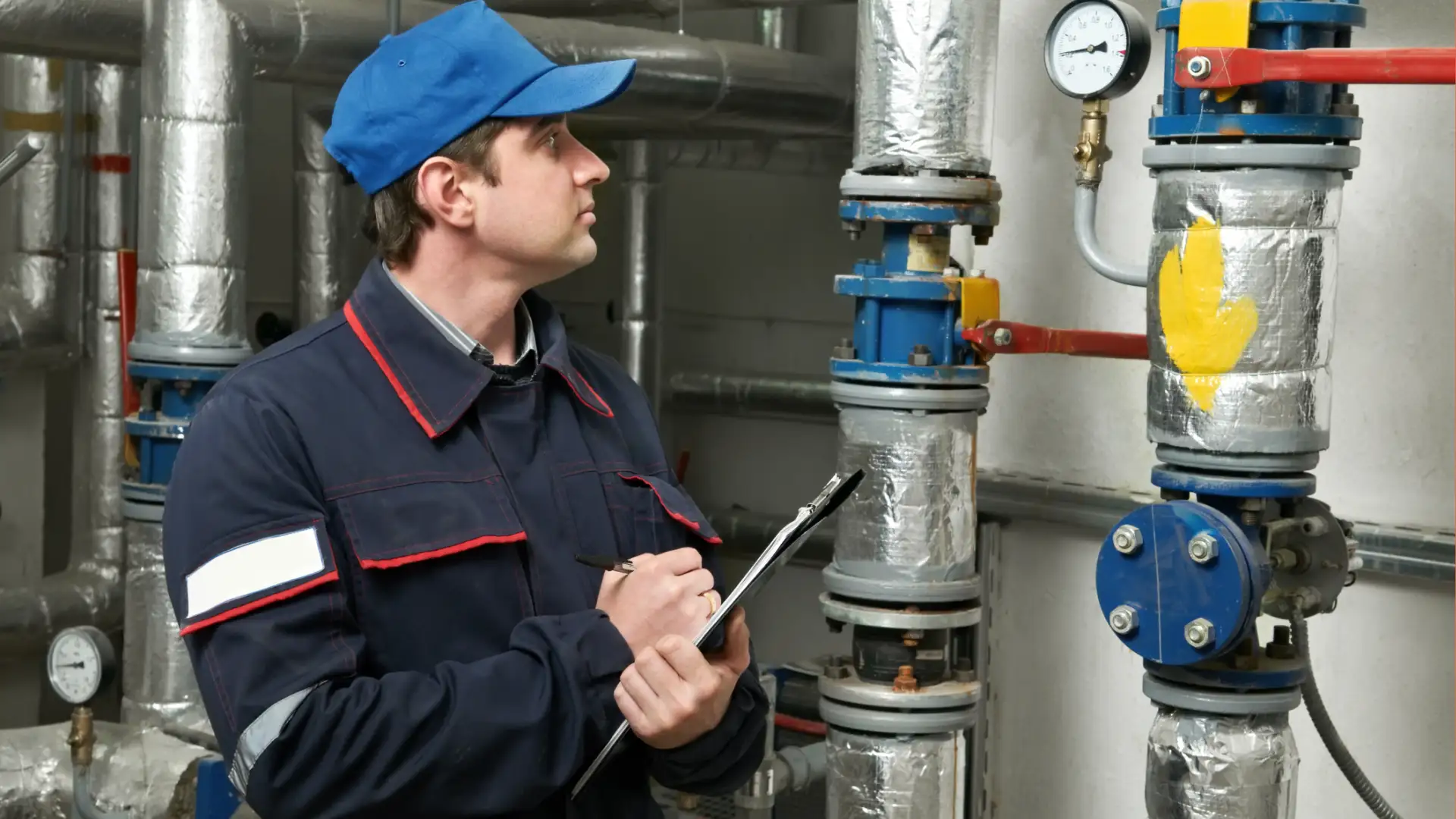
In facilities management, staying ahead of problems is half the battle.
Preventive maintenance (PM) helps facility teams shift from putting out fires to planning for long-term performance—especially across multi-site operations. If you’re looking to improve consistency and reduce costs across locations, Fexa’s Preventive Maintenance solution and this in-depth Preventative Maintenance Guide offer practical frameworks.
Preventive strategies also enable smarter asset planning. Discover how preventive maintenance and asset tracking reduce waste and improve uptime for facilities with complex operations.
How does preventive maintenance improve operational efficiency in multi-site facilities?
Multi-site facilities face unique logistical challenges. Uncoordinated maintenance efforts across locations can lead to inconsistent performance, disjointed service histories, and underutilized technician resources. Preventive maintenance addresses this by creating repeatable, scheduled workflows that keep equipment running efficiently—no matter the site.
With standardized PM processes in place, facility managers can minimize disruption, improve technician productivity, and reduce the need for emergency repairs. Tasks such as scheduled HVAC servicing, electrical inspections, and plumbing checks can be performed proactively, avoiding costly surprises and helping operations run smoothly across all sites.
What impact does PM have on cost savings and asset longevity?
One of the most immediate benefits of preventive maintenance is its ability to lower long-term costs. Rather than dealing with expensive breakdowns or urgent part replacements, PM helps facilities stay ahead of wear and tear. Regular upkeep—such as lubrication, calibration, and minor part swaps—can significantly extend the lifespan of assets like refrigeration units, mechanical equipment, and HVAC systems.
Additionally, maintenance budgets become more predictable under a PM model. Organizations avoid the financial strain of emergency services and reduce the need to prematurely replace assets that could have been salvaged through routine care. When paired with asset tracking tools, facility managers can also make smarter “repair vs. replace” decisions, improving capital planning and reducing waste.
How does it help meet compliance and sustainability goals?
Facilities must meet a growing number of environmental, safety, and operational regulations. Preventive maintenance plays a critical role in staying compliant. Regular inspections and service records help ensure that assets like fire suppression systems, HVAC units, and refrigeration equipment remain within regulatory thresholds.
PM also supports sustainability initiatives. Well-maintained systems consume less energy, generate fewer emissions, and reduce the need for raw materials due to premature part replacement. Preventive upkeep ensures efficient operation, helping organizations align with green building standards and internal sustainability targets—especially when equipment data is centralized and monitored through a CMMS.
How does preventive maintenance reduce risk across distributed facilities?
Risk multiplies when maintenance is inconsistent or undocumented. Without a structured preventive program, issues at one site can quickly become systemic across an organization. Whether it’s failing HVAC units during peak seasons or safety equipment that doesn’t meet inspection standards, reactive maintenance introduces operational and reputational risks.
PM helps mitigate these risks by creating a consistent approach to asset care. Facility managers can ensure that every location follows the same maintenance protocols, maintains updated service logs, and meets scheduled inspection intervals. This minimizes the likelihood of surprise failures, non-compliance penalties, or safety incidents—especially in industries like healthcare, retail, or food services where uptime and safety are non-negotiable.
Why is a modern CMMS critical to scaling preventive strategies across locations?
Scaling preventive maintenance across multiple facilities is nearly impossible without the right tools. A modern Computerized Maintenance Management System (CMMS), like Fexa, brings structure, automation, and visibility to your strategy.
With CMMS software, teams can:
- Standardize preventive maintenance schedules across all locations
- Automate recurring work orders based on time or usage
- Track asset health and service history in real time
- Manage technician workflows and vendor performance
- Access mobile tools for on-site task execution
CMMS platforms eliminate the inefficiencies of paper-based processes and siloed spreadsheets. By centralizing data, automating routine tasks, and delivering insights through dashboards, facility teams can make smarter decisions and optimize performance—at scale.
Want to go deeper? Fexa’s guide to facilities management software and CMMS breaks down the features and benefits that matter most when managing large, distributed portfolios.
Ready to future-proof your facilities?
Preventive maintenance is no longer optional—it’s a strategic imperative for managing cost, risk, and operational performance across complex facilities. With the support of modern tools like Fexa’s CMMS, your team can turn maintenance from a headache into a competitive advantage.
Learn more about Fexa’s Preventive Maintenance Solution: https://fexa.io/preventative-maintenance